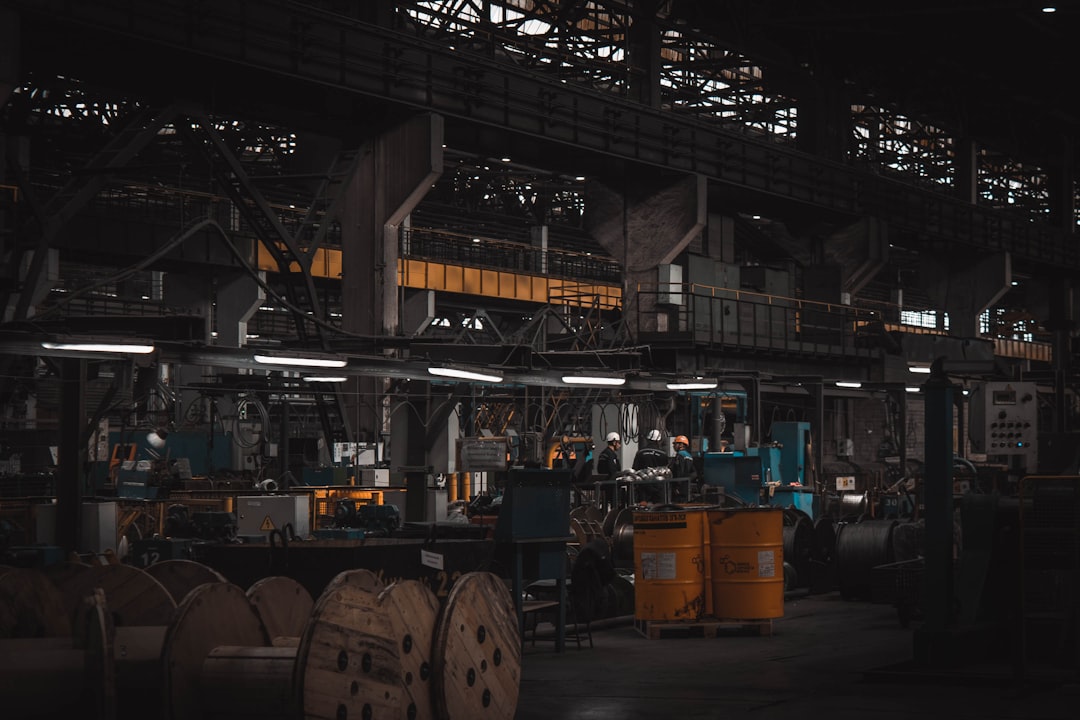
In the world of industrial automation, machinery, and electronics, connectors may seem like minor components. However, they play a critical role in ensuring reliable power and signal transmission. Choosing the right industrial connector isn’t just a matter of plug-and-play — there are multiple factors that technicians, engineers, and procurement teams must consider. Selecting the wrong type can lead to system failures, increased maintenance costs, and even safety hazards.
Below are five key factors to consider when choosing industrial connectors, to help you make informed decisions that support long-term performance and operational efficiency.
1. Environmental Conditions
One of the most important considerations is the environment in which the connector will be used. Industrial settings often expose components to extreme temperatures, moisture, dust, and chemicals. A connector that works well in a clean, controlled environment may fail quickly in a dusty or corrosive facility.
- Temperature resistance: Ensure the connector can operate within the full range of temperatures it will be exposed to.
- Ingress protection (IP) rating: A high IP rating guarantees protection against solids and liquids. For example, an IP67 rating means the connector is dust-tight and protected against immersion.
- Vibration and shock resistance: If you’re working with heavy machinery or vehicles, the connector must withstand constant movement.
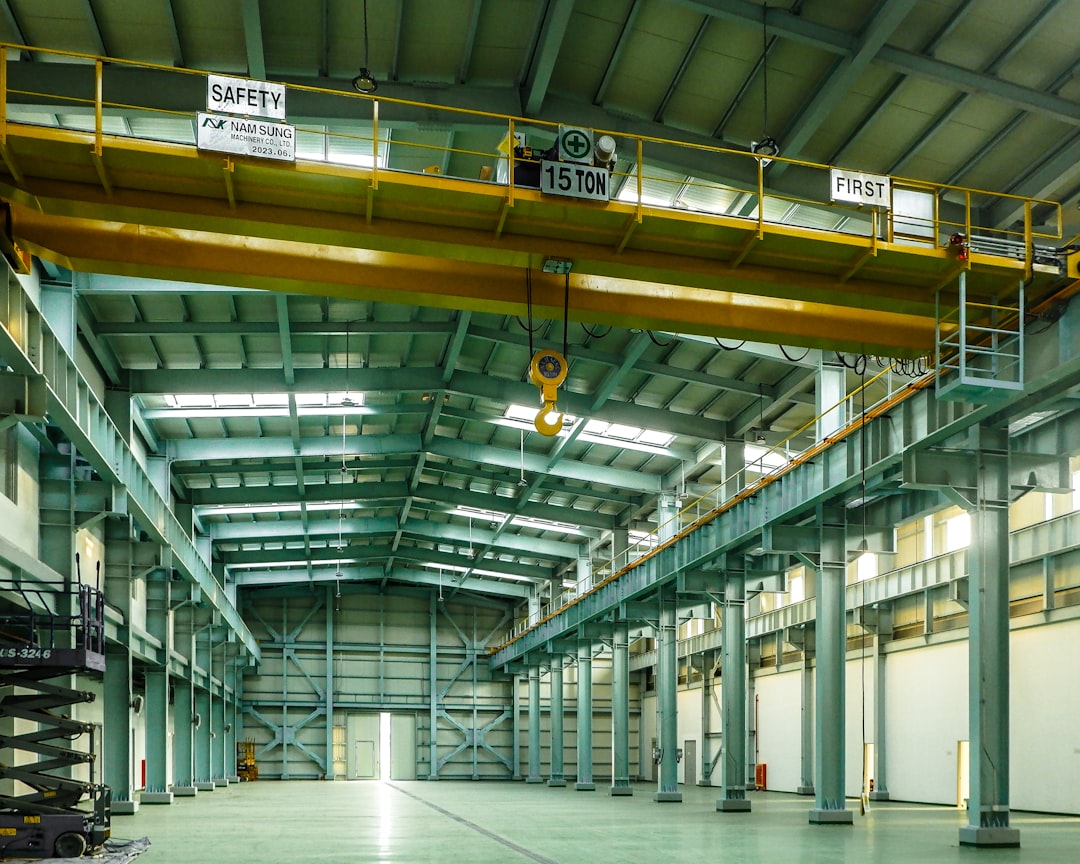
2. Electrical Specification Requirements
Matching a connector to its intended electrical workload is essential. Ignoring specs like current load, voltage ratings, and signal type can lead to overheating, signal loss, or even fire hazards.
- Current and voltage rating: Choose connectors compatible with your system’s amperage and voltage.
- Contact resistance: Lower resistance connectors improve efficiency and reduce heat generation.
- Signal integrity needs: For data transmission, especially in industrial Ethernet or fieldbus systems, make sure connectors support the required bandwidth and frequency.
3. Connector Type and Compatibility
With numerous connector types available — including circular, rectangular, modular, and more — it’s essential to pick one that fits both physically and functionally within your system.
- Pin count and layout: Check that the number and configuration of pins match your requirements.
- Gender and mating type: Ensure compatibility between male and female connectors for seamless mating and unmating.
- Keying and coding: Helps prevent incorrect connections, especially in multi-connector setups.
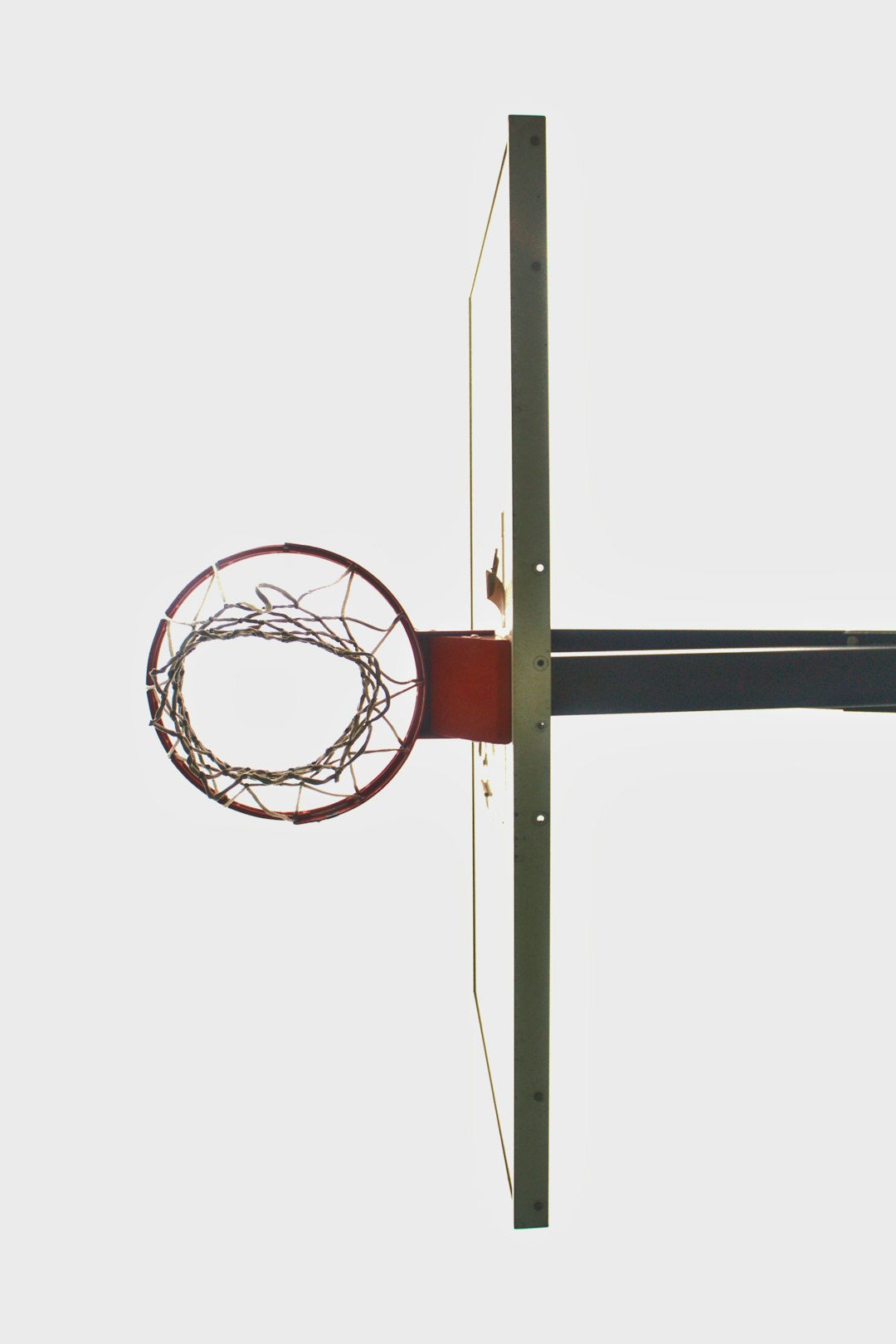
4. Durability and Maintenance
In industrial applications, connectors are often subject to repeated mating cycles, exposure to wear and tear, and eventual degradation. Durability affects both lifecycle cost and system uptime.
- Mating cycles: Choose connectors rated for frequent connections and disconnections if necessary.
- Material quality: High-grade alloys and corrosion-resistant coatings extend lifespan.
- Ease of maintenance: Some models offer modular designs or allow quick swaps, saving time during repairs.
5. Compliance and Industry Standards
Compliance with industry and international standards is crucial — especially in industries like automotive, aerospace, and medical, where safety and reliability are paramount.
- Certifications: Look for UL, CE, RoHS, or ISO certifications to ensure quality and safety.
- Industry-specific standards: Different sectors may require compliance with MIL-SPEC, IP-rated, or other specialized connector standards.
- Traceability and documentation: Opt for suppliers offering clear product data and traceability to make audits easier.
Finally, working with reliable manufacturers and suppliers that offer technical support is indispensable. They can assist with product selection, customization, and integration to ensure your connector solutions meet both current and evolving needs.
Choosing the right industrial connector is more than just a technical decision — it’s a strategic one. By considering these five key factors, you can reduce downtime, enhance safety, and optimize the performance of your equipment and systems in the long run.